When it comes to metal wire mesh, distinguishing between electro galvanized and hot dip galvanized can be crucial. In this post, we will delve into the nuances of these galvanization methods and shed light on their respective merits.
Galvanized technology is renowned for its rust-proof properties, making it an essential treatment for metal screen mesh in various applications. While both electro galvanized and hot dip galvanized offer rust resistance, the latter boasts a higher zinc coat and superior longevity. However, customers often express concerns about the authenticity of the galvanization process, as hot dip galvanization incurs higher costs compared to its electro counterpart. Addressing these concerns not only empowers customers but also fosters healthy market competition between customers and manufacturers.
To understand the differences between the two methods, let's delve into their respective processes. Hot dip galvanizing involves a series of steps, including wire oil removal, acid washing, immersion in medicine liquid, drying, immersion in zinc liquid, and extraction. On the other hand, electro galvanizing, also known as cold galvanizing, employs electrolysis equipment to eliminate wire oil, followed by acid washing, immersion in zinc liquid, and electrolysis connection. Through the directional movement of electricity, a layer of zinc is formed on the wire. While a chemical composition test is the most accurate means of identifying the zinc rate, experience-based identification becomes crucial in the absence of suitable testing conditions.
In terms of appearance, electro galvanized wire mesh exhibits a smooth, bright surface with yellow and green hues, often appearing colorful due to the passivation process. The use of white passivation can result in a bluish-white or white/green zinc coat, showcasing a slight iridescence when exposed to sunlight at specific angles. Over-burnt wires may yield thicker zinc coats, while internal corners with insufficient electricity may result in thinner coats. Ideally, the wire mesh should be devoid of any zinc lumps.
In contrast, hot dip galvanized wire mesh appears rougher and darker with a silver color. It may exhibit watermarks and occasional tumors on the surface, especially at the wire ends. However, the zinc coat thickness and corrosion resistance of hot dip galvanized wire mesh far surpass those of its electro galvanized counterpart. While electro galvanized wire mesh offers a brighter and smoother look, its thin zinc coat compromises its corrosion resistance.
In conclusion, discerning the relative merits of galvanized technology can be deduced from the appearance. Superior galvanization techniques yield a uniform zinc coat without any omissions, whereas inferior techniques display the opposite characteristics.
For all your wire mesh needs, trust in Maishi - your reliable partner in quality and innovation. Contact us today to explore our comprehensive range of galvanized wire meshes.
#WireMesh #GalvanizedTechnology #Maishi
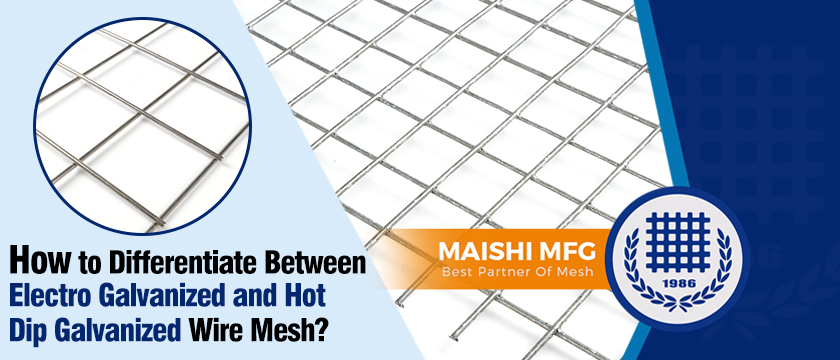
Leave a Comment